The Impact of Cement Quality on Long-Term Infrastructure Durability
08.07.2025
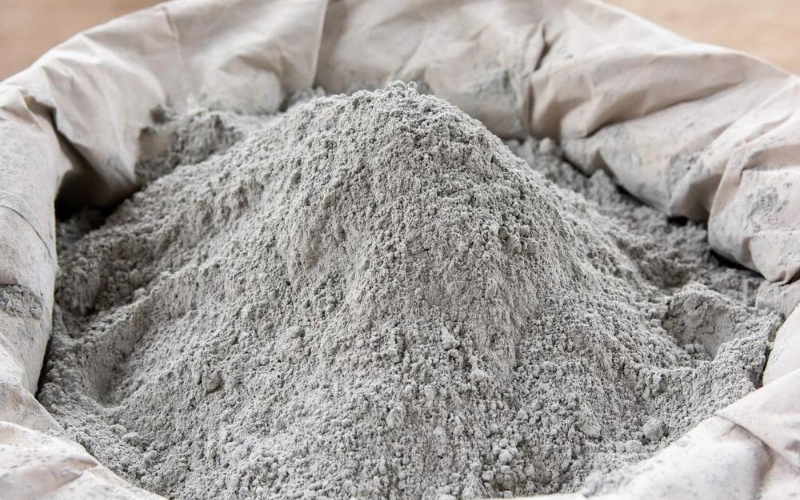
Cement is the fundamental binding material that holds the modern world together. From skyscrapers to highways, its quality directly influences the lifespan and resilience of infrastructure. Poor-quality cement can lead to structural weaknesses, costly repairs, and even catastrophic failures over time.
Understanding how cement quality affects infrastructure durability is essential for engineers, builders, and decision-makers. This article explores the key components of cement quality and how they impact the long-term performance of various infrastructure projects.
1. The Role of Cement in Infrastructure
Cement acts as the core binding material in concrete, mortar, and other construction mixtures. Its primary function is to react with water in a process called hydration, forming a hard matrix that binds aggregate materials like sand and gravel. This hardened mass becomes the structural foundation for countless infrastructure types, including bridges, roads, dams, tunnels, and buildings.
Since cement is involved in nearly every critical structure, its quality directly determines the strength and integrity of these assets. Long-term exposure to environmental stresses like water, temperature fluctuations, and chemical agents requires the cement to maintain stability and resistance over decades.
2. Key Indicators of Cement Quality
High-quality cement is evaluated through several chemical and physical properties. These include:
- Compressive strength: The ability to withstand loads without failing is the most direct indicator of cement performance.
- Setting time: Proper initial and final setting times are crucial for effective workability and curing.
- Fineness: Finely ground cement particles provide a larger surface area for hydration, improving strength development.
- Chemical composition: Balanced proportions of lime, silica, alumina, and iron oxide determine long-term stability and resistance.
- Soundness: Resistance to expansion caused by excess free lime or magnesia ensures that the structure doesn’t crack or deform.
All of these parameters contribute to the durability and reliability of infrastructure over time. Cement that fails to meet these benchmarks can result in premature degradation.
3. Long-Term Effects of Poor Cement Quality
When cement quality is compromised, the consequences can be severe. One of the earliest signs of failure is cracking due to shrinkage, poor curing, or weak bonding. These cracks allow moisture to penetrate the structure, accelerating corrosion of embedded steel reinforcements.
In aggressive environments, such as coastal or industrial regions, low-quality cement can suffer from sulfate attacks, alkali-silica reactions, or carbonation. These chemical reactions compromise the cement matrix and reduce the structure’s ability to bear loads. Over time, this results in increased maintenance costs or total replacement.
4. Influence on Specific Infrastructure Types
The impact of cement quality can vary depending on the type of infrastructure:
- Bridges: Require high resistance to dynamic loads and water ingress. Substandard cement increases risk of spalling and corrosion.
- Roads and highways: Poor cement leads to surface cracking, rutting, and failure under heavy traffic.
- Dams and water-retaining structures: Inferior cement may not resist hydrostatic pressure and chemical erosion, causing seepage and weakening.
- Tunnels: Face continuous exposure to groundwater and stress loads. Low-quality cement undermines tunnel lining integrity and safety.
In each case, long-term performance is directly tied to the chemical composition and production consistency of the cement used.
5. Quality Control in Cement Manufacturing
Ensuring cement quality begins at the manufacturing stage. Cement production involves precise control of raw materials, kiln temperatures, and grinding processes. Advanced quality assurance methods include:
- X-ray fluorescence (XRF) analysis: To monitor raw material composition.
- Blaine fineness testing: To control the particle size distribution.
- Compressive strength testing: To evaluate cement batches before shipment.
Manufacturers adhering to international standards such as ASTM, EN, or ISO ensure more reliable and durable cement. Lack of proper quality control in the manufacturing process can introduce variability that leads to unpredictable performance in the field.
6. The Impact of Admixtures and Additives
Cement quality is not only about the core material but also how it interacts with additives and admixtures. These include fly ash, silica fume, slag, and plasticizers, which are used to modify performance characteristics.
When mixed with high-quality cement, these additives can significantly enhance durability, reduce permeability, and improve resistance to environmental attacks. However, when combined with low-quality cement, the benefits are often negated, and interactions may even lead to instability.
7. Sustainability and Lifecycle Considerations
Durable infrastructure minimizes environmental impact by reducing the need for frequent repairs and replacements. Cement that supports long-term performance contributes to sustainable construction practices and optimized lifecycle costs.
High-quality cement reduces the carbon footprint of infrastructure by extending usable lifespan, conserving materials, and minimizing energy use during renovation. Conversely, low-quality cement increases total emissions through repeated maintenance and shorter service cycles.
8. Innovations for Enhancing Cement Quality
Modern advancements in cement technology aim to improve both performance and environmental compatibility. These include:
- Nanotechnology: To engineer cement at the molecular level for superior strength and durability.
- Smart sensors: Embedded in concrete to monitor curing and long-term structural health.
- Green cement: Using alternative materials like geopolymers or carbon-capturing cement formulations.
Such innovations reinforce the role of cement quality in building the resilient infrastructure of the future. They also reduce variability and human error by automating many of the quality control processes.
9. Field Testing and Real-Time Monitoring
Post-construction durability assessments often rely on real-time monitoring systems. Sensors embedded in concrete can track temperature, humidity, strain, and corrosion activity. These data help in assessing whether the cement and overall structure are performing as expected.
Furthermore, periodic non-destructive testing like ultrasonic pulse velocity, rebound hammer tests, or core sampling provides ongoing insight into the integrity of the structure. These evaluations are especially valuable in critical infrastructure like high-speed rail systems, tunnels, and nuclear facilities.
10. Best Practices for Infrastructure Planners
To ensure long-term durability, infrastructure planners and engineers should:
- Select cement suppliers with certified quality control systems.
- Specify appropriate cement types for environmental conditions (e.g., sulfate-resistant cement for coastal regions).
- Use proper curing methods to maximize cement hydration and strength development.
- Implement lifecycle assessment during the design phase to evaluate durability needs and maintenance expectations.
These steps can prevent the hidden costs of using poor-quality materials and ensure public safety and financial efficiency.
Conclusion
The quality of cement is a foundational element in the success and longevity of infrastructure projects. It determines not only the strength and appearance of a structure but also how it ages under stress, weather, and time. Choosing high-quality cement and maintaining strict quality standards throughout the construction process is essential for building a durable and sustainable built environment.
In an era where resilience and sustainability are key, cement quality should never be compromised. Investment in better materials today leads to stronger, longer-lasting infrastructure tomorrow.